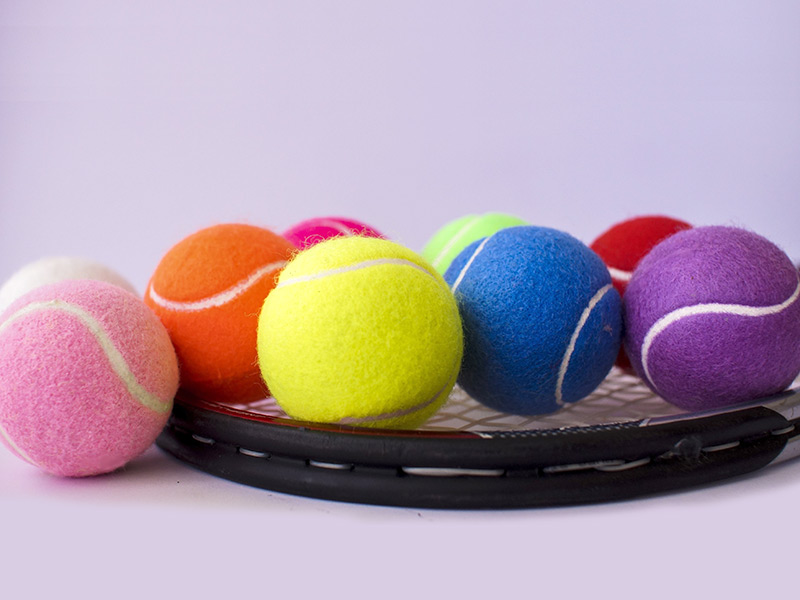
Manufacturing Process
Fu-Jen has solid skills in the scaled production of high-quality sports rubber ball products ranging from match level to training level. Our goal is to become an efficient and smart factory with highly flexible production lines, creating more value for our clients by providing various options for customization. By introducing automated manufacturing and inspection equipment, we can achieve a small-volume large-variety production system, which enables us to face the ever-changing market and to reach the mutual success of our clients.
There are two kinds of production lines according to our products. For different products and specifications, we have developed a full range of flexible production systems, ensuring that all products meet the international quality standard. We break down the manufacturing process into six stages, which include Rubber Mixing, Half-shell Forming, Core Forming, Felt Forming, Assembly, Stamping & Packaging. Among all, the âFelt Formingâ and âAssemblyâ are tennis ball only processes.
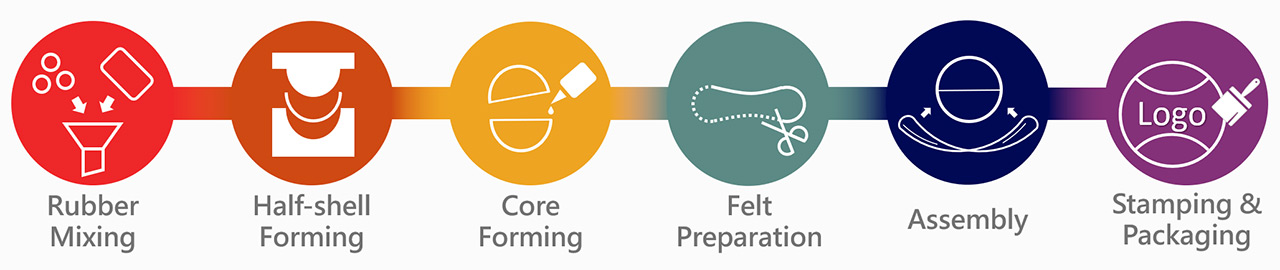
Steps
Rubber Mixing:
The first step of rubber mixing is designing the formula of the rubber according to the specification of the ball. After weighing the rubber and other chemicals, we mix them evenly in a rubber mixer.
Half-shell Forming:
We place the grains inside the mold of a hydraulic pressing machine for the first curing, where the grains form into half-spherical shapes (half-shells) under certain conditions.
Core Forming:
We synthesize a unique adhesive and use it to glue the half-shells. In the second curing process, two half-shells merge permanently into a core. This is the final stage of manufacturing for regular rubber balls.
Felt Preparation (Tennis balls only):
The fabric is cut into dumbbell-shaped in an automated cutting machine. The shape of the felt is designed according to the size of the tennis balls, so that the felt fits the surface of the ball nicely.
Assembly (Tennis balls only):
In the last manufacturing stage of tennis balls, the glued cores and felts are assembled by hand or by machine. The balls move on to the third curing process, where cores and felts stick firmly together.
Stamping & Packaging:
In the last stage, the well-produced and examined products are stamped with the logo or trademark. We pack the balls in response to customized packaging, and deliver the product to our customers as soon as possible.
Gallery
- The rubber is precisely mixed to reach the optimum performance of each ball.
- The rubber forms into half-shell shape under high temperature and pressure.
- With special glue applied, two half-shells merge in a hydraulic machine.
- In the process of tennis balls, the neatly cut felts are coated with white glue.
- Consist of two felts and a core, a tennis ball is nicely produced in this stage.
- After logo stamping and customized package, the product is ready to go.